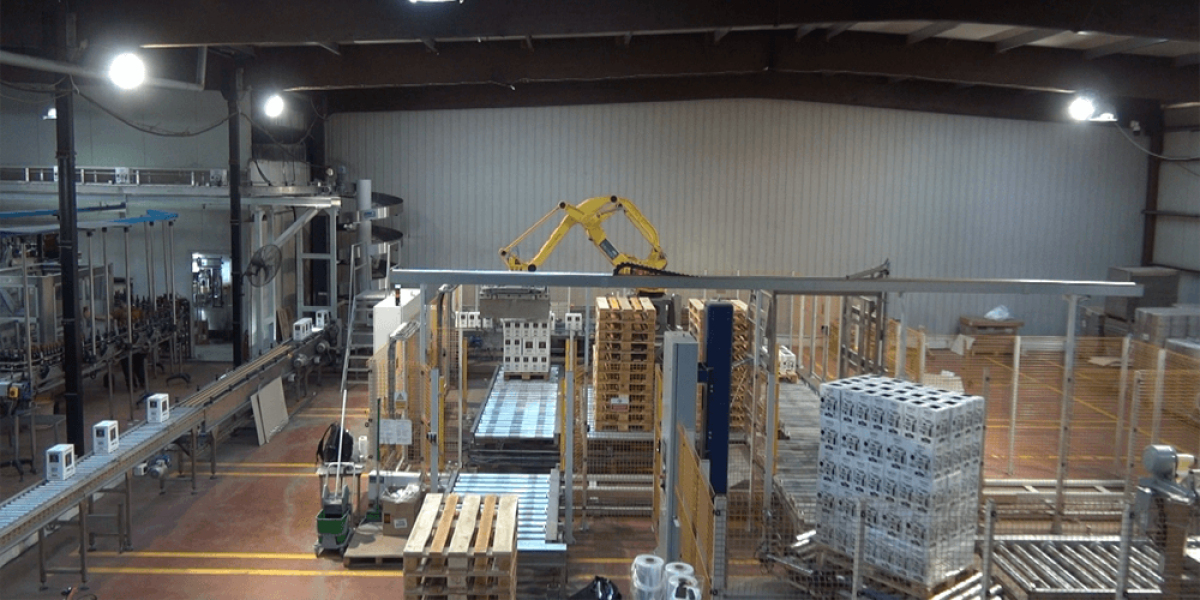
Theodorou Group, with great expertise in robotics, automation and Industry 4.0 digital transformation solutions, designed and implemented a complete system for the full automation of Cavino’s production processes, with robotics systems, End-Of-Line Automation, MES Tracer Factory & full IT interface systems and production equipment, resulting in the ultimate digital factory of the Industry 4.0 era.
The Client
Cavino, which was founded in 1958, is located on the slopes of Aigialia, amid charming vineyards. It produces wines that are distributed throughout Greece and in 50 countries all over the world. Its wines have won awards in international competitions and from world-class reputable wine writers and critics.
The company, closely following the modern developments of the time, has been modernized in recent years with state-of-the-art technological equipment in all areas of production. Four new bottling lines took over to ensure the quality of the wines and spirits (ouzo, tsipouro and brandy), at the same time that air-conditioned storage areas of 5,000 m2 took over their ideal storage over time.
The Need
Theodorou Group actively participating in technological developments and aiming to ensure the provision of modern and reliable solutions in the industry, listens to the needs of the factories of the future and proceeds with applications to cover them. The modern winery & distillery of Cavino, in collaboration with Theodorou Group, proceeded to implement and install a set of communicating applications and equipment, with the aim of digitizing production processes, the complete management of the final products at all levels of their packaging, the elimination of errors in the production process, increasing the efficiency of the production lines, resulting in greater flexibility, reducing costs and increasing the profit margin.
The Solution
In order to cover the above need, the basic and initial installation was carried out by the company Zenon Automation SAICT of Theodorou Group for the complete automation of the End-of-Line management of two production lines. The solution included the products handling from the production machines, the dynamic weighing and marking of the products to perform smart sorting using cameras, based on the production and sales order, with the aim and result of ensuring uninterrupted proper operation and the smart delivery of pallets in particular short times. At the same time, modern IIoT communication tools and MES (Manufacturing Execution System) industrial software solution functionalities were used to enable digital transformation, smart production management and two-way data transfer between IT systems and production equipment.
As a result, the company was able to have full real-time monitoring of quantitative and qualitative elements of production execution and development, with continuous control of correct execution at various production stages, automatic updating of production equipment with the necessary information for the orderly and correct execution of production and finally the automatic systemic delivery of the finished products to the company’s warehouses, simultaneously informing all those involved in multiple departments of the company.
In practice, a customer order (sales department) arrives with the minimum possible operational steps to be captured and automatically executed on bottling and palletizing lines of finished product for sale (production department), with automatic systemic delivery of the finished products produced in the warehouse to be shipped to the customer (logistics department).
The Benefits
- Dissemination of valid information between the company’s departments
- Drastic reduction of human errors in the production area
- Reduction of set-up and change-over times, with automatic adjustment of palletizing patterns, product marking printers, leading to a drastic reduction in rejects
- Paperless production, with the elimination of production forms and manual accounting entries
- Real-time monitoring of production status and progress
- Flexibility and ability to make timely decisions, based on valid data
- Increasing available production time of machines, as well as ensuring and increasing production quality
- Ensuring full traceability of the final product reaching the consumer
- Identification of meaningful action plans to improve production processes and lines
If you are interested in a similar solution, please call us on tel. +30 210 6690900 or fill out the contact form below.
Food / Beverages