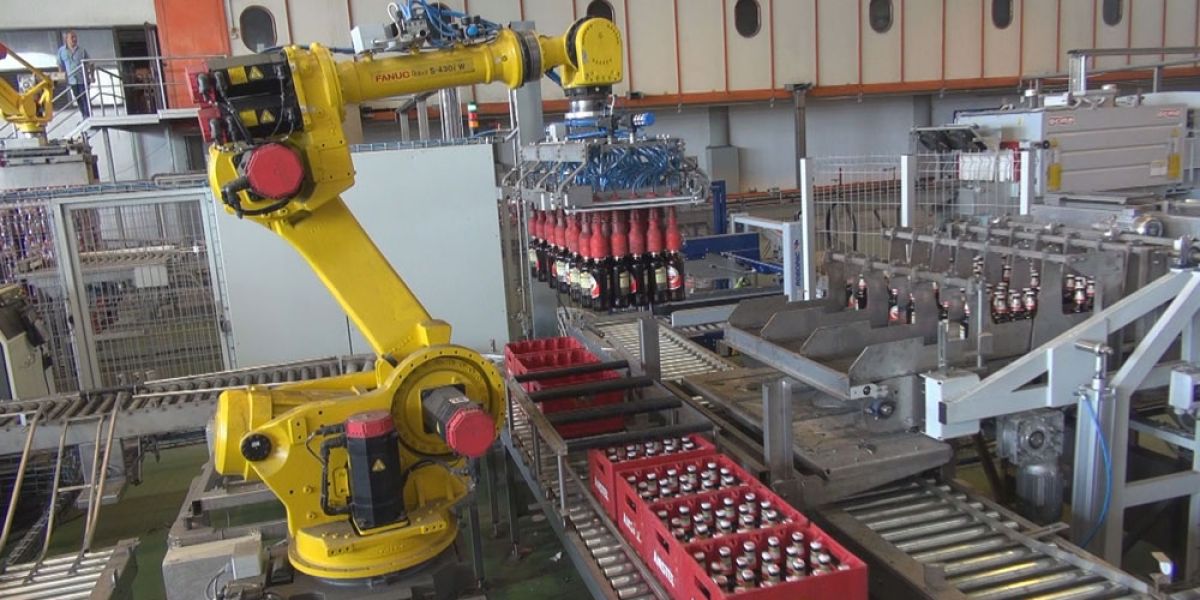
ZENON AUTOMATION SAICT, a company with extensive experience and expertise in the design and implementation of robotic and automation solutions for the end-of-line, has successfully completed the installation of a fully automated repackaging line of glass bottles for ATHENIAN BREWERY. ATHENIAN BREWERY is a leading company in the Greek beer market with a wide portfolio of brands such as Amstel, Amstel Pils, Amstel Bock, Amstel Radler, Heineken, Alpha, Fischer, a.o.
The Need
ATHENIAN BREWERY was seeking a fully automated repackaging line of glass bottles from plastic crates into shrinked bundles of multipacks.
The implementation required the de-palletizing of plastic crates, the de-crating of plastic crates and the feeding of glass bottles to a multipacks machine. The multipacks had to be shrinked into bundles, coded and palletized. Furthermore the pallets had to be shrinked wrapped and grouped before being removed from the system. A further need was this of creating mixed six-packs containing two different products (4+2). The line was also required to have a secondary function, this of case packing the bottles instead of creating multipack bundles.
The solution had to meet the needs for high productivity and optimal utilization of space and existing resources.
The Solution
ZENON designed and offered an integrated and fully automated solution that fully met the needs of ATHENIAN BREWERY. The repacking line that was built had the following features:
- Depalletizing of full crates
- Palletizing of empty crates
- Decrating of full crates
- 1st level packaging of bottles into shrinked multipacks
- Coding of multipacks (expiry date, Lot number)
- 2nd level packaging of multipacks into shrinked bundles
- Labeling of bundles (expiry date, description, barcode)
- Palletizing of bundles
- Stretch wrapping of bundle pallets
- Supervision and control system
For the secondary function of the line:
- Case erecting of carton boxes
- Case packing of de-crated bottles
- Case sealing of carton boxes
Three robotic cells were designed and built by ZENON for the needs of the above system: one for the de-palletizing of the full crates and the palletizing of the empty crates, one for the de-crating of the bottles and case packing of bottles and one for the palletizing of the shrinked bundles. It is worth mentioning that 3 existing robotic arms, modified and adjusted to the needs of the project, were incorporated in the system, thus dramatically reducing the cost of the project.
The entire packaging line also consists of: two shrink wrapping machines, a case erector, a case sealer, an industrial inkjet printer, a label print and apply system, a stretch wrapping machine and a complete product handling system.
Further to the design, construction and integration of the solution, ZENON developed a SCADA system which allows the synchronization and smooth operation of the entire system. This IT system also allows the graphic representation, supervision and control of the line and its productivity in real time, and it provides meaningful data about the production. The design of the solution ensures ease-of-use, adaptability to future needs and high productivity.
The control panels of the system are equipped with touch screens with various capabilities such as error display and graphic presentation of system performance and remote technical support. The system has a variety of production programs preinstalled to cover the needs of different products therefore product changeovers are automatic and immediate without any need to change any settings, beyond the simple choice of the product.
It is important to note that a multi-zone safety system was especially developed to cover the needs of the application thus ensuring its compliance both with CE norms and the customer’s strict specifications without compromising the productivity of the line.
Benefits
- Increase in productivity (up to 21,000 bottles/min)
- Production cost reduction
- Reliability and minimum maintenance needs
- Flexibility and expandability as the system can easily be upgraded and modified to handle new products
- Optimal resources utilization (space, manpower, existing equipment and IT)
- Minimum operating requirements
- Errors minimization
- Fast and accurate after sales support
If you are interested in a similar solution, please call us on tel. +30 210 6690900 or fill out the contact form below:
Food / Beverages