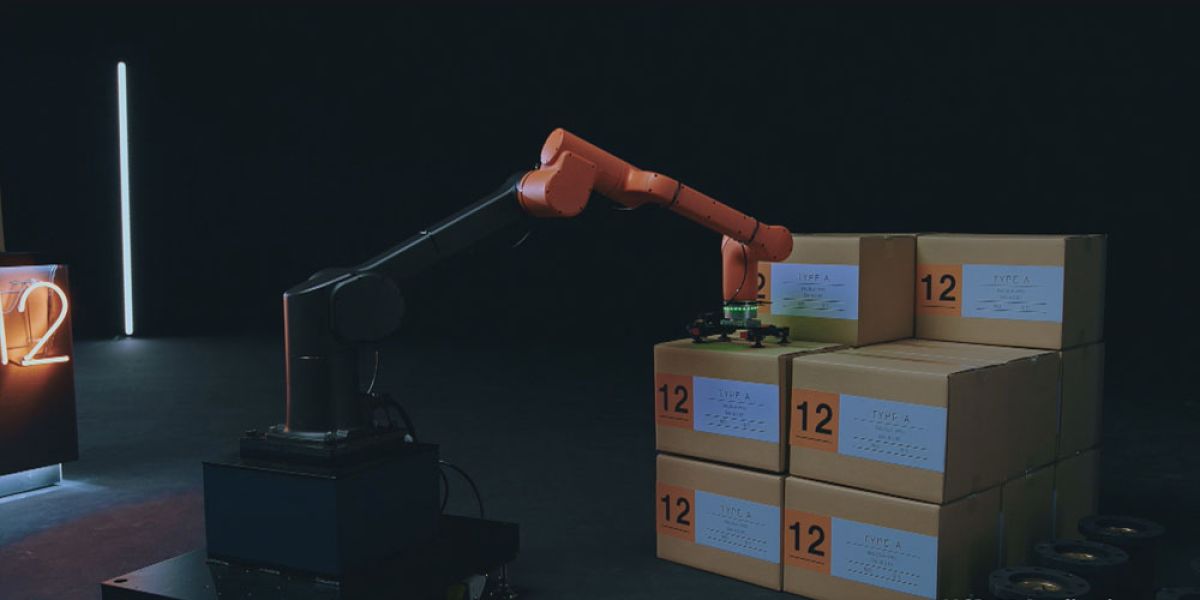
Marios Hadjiandreou, Ph.D. (Cambridge)
Theodorou Group Director, Business Developer
The C-19 pandemic is an extremely important challenge, with consequences for the health of the citizens, the economy of the country, but also of each company separately. The C-19 has changed the way we deal with our friends or colleagues at home, on the street, in the office, in the factory. It has changed the way a business operates, while the new conditions that have been created are a challenge for the next day.
Automating the operations of a business, in the case of a factory or warehouse, was basically the prerogative of large companies that had the necessary capital (and patience) to make such investments. In most Greek factories, the automation stops in the primary packaging (ie in the product itself), in several cases it extends to the secondary packaging (eg box), and in rarer cases to the tertiary (pallet). No reason to automate the warehouse, while even the largest logistics centers are based almost entirely on humans.
The new conditions in the post C-19 era, make “automation” an urgent need in all stages of operation of a factory (import of raw materials, production, storage, order execution and shipment) and for all companies, regardless of size their. Moreover, the new solutions offered in automation and robotics are now significantly lower cost, allowing their introduction in all companies, small or large.
Ideas for increasing competitiveness & flexibility in the post-Covid era
Here are some ideas that deserve the attention of business executives, in order to “shield” the business and increase its competitive advantage in an ever-changing era:
Robots have for decades found applications in industry and logistics, to perform various tasks such as automatic palletizing / unpacking, automatic boxing, and automatic picking & sorting. In the age of the new robotics, robots are faster, positioning accuracy and repeatability are increased, while their drivers become more and more intelligent and offer much more flexibility and interface with other robots, machines and central information systems. In other words, robots are now an integral part of the digital factory.
At the same time that robots are becoming smarter, the cost per unit has been significantly reduced and there are also standardised robotic modules available for specific applications (eg carton palletizing, plastic can boxing, etc.). A new trend is the ability to move the robot itself, thus serving more lines or functions, existing or even future, which achieves greater economy and flexibility. The result is the ability to introduce robotics to ever smaller “smaller” companies.
Another important development is the appearance of collaborative robots or cobots. Cobots are a new generation of robots that are designed to work harmoniously with humans in a common workplace without the risk of injury to perform various repetitive tasks. For example, they can undertake tasks such as packaging (shaping, boxing, palletizing, etc.), quality control, machine operation, but also picking and sorting products.
Unlike traditional industrial robots which are usually much larger in size and capacity and are designed to operate autonomously and isolated from humans in enclosed spaces, cobots work side by side with no infrastructure required on fences or security bars! The installation of a cobot system is very easy (within a few hours) and can work almost anywhere, covering future business needs. With cobots, productivity is achieved, maximum security and great flexibility are achieved, while the coexistence of robot & human has a very positive effect on the performance of the employee himself.
The benefits of cobots are manifold when combined with other technologies such as autonomous mobile robots (AMRs). In a factory, workers travel tens of kilometers daily transporting materials from one place to another (raw materials, semi-finished products, ready-made, spare parts, etc.). AMRs are self-propelled robots that move intelligently in the factory or warehouse area and handle the transportation of various materials, freeing up significant creative time for employees.
For example, in a factory they can supply the machines and / or transport the finished products for storage while in an e-commerce warehouse they transport products to the order-processing station (goods-to-person). A robot is capable of multiple tasks on the same day while working harmoniously both with humans (as with cobots, AMRs are completely safe) and with a fleet of other robots.
AMRs have a complete view of the space and, unlike other motor vehicles, have the ability not only to stop if something interrupts their course but also to calculate on the spot the next optimal route. The acquisition cost in relation to the offered value is very low, that is why the amortization of such an investment is very fast.
As is well known, the C-19 pandemic has accelerated the growth of e-commerce, at a faster pace than expected. The immediate consequence is that companies, which were not prepared for this development, are looking for solutions for the most immediate execution of the large volume of orders they receive daily. Equipment solutions, as we have described above, but also more “advanced” order fulfillment software packages.
Upgrading to a new WMS at the moment involves risks, as in addition to the cost and implementation risk, it takes a long time to learn. To that end, Zebra Technologies has created the Zebra FulfillmentEdgeTM, a combination of fulfillment software and wearables (smart glasses, bracelets, etc.) that guide and assist employees in picking, packing, shipping, and stocking. For example, when entering a new order, FulfillmentEdgeTM processes real-time data from the WMS and suggests who should execute it and when, while at the same time, through smart wearables, gives the picker instructions for its most efficient execution. Most importantly, the FulfillmentEdgeTM can be easily & quickly integrated on existing WMS, does not involve any risk and is an excellent management tool as it offers a complete picture of the effectiveness of the team and each employee individually. Increase efficiency by using FulfillmentEdgeTM is at least 25%!
In conclusion, in this difficult time when the global economy is being “tested” by the C-19 and market trends are changing faster than technology itself, companies need to handle the situation properly and seize opportunities that may be presented. The ideas we propose are immediately applicable, do not require much implementation time or cost and their biggest advantage is the flexibility they offer to the business. After all, we live in an era that is constantly changing and in which the leading role will be played by companies that have both the mood and the flexibility to change!
Dr. Marios Hadjiandreou is Theodorou Group Director, Business Developer.